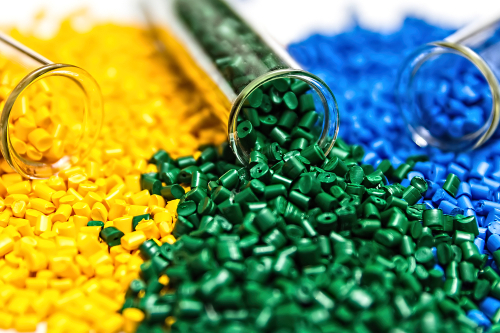
When designing your plastic components, whether on paper or in 3D printing software, you will eventually want to have your parts mass produced. But before you can mass produce plastic parts you will need to have a custom injection mold created to make sure that your parts can be replicated quickly and without error. In order to optimize your design for this process, you should take note of these 5 common design errors.
1. Not Designing For Custom Injection Molding
This is a bit of a catch-all, but it is worth mentioning. When you design your plastic components, your designs need to be made with manufacturing in mind. In order to avoid not designing with manufacturing in mind, you should work on your designs with an experienced plastic manufacturer. If you are new to designing custom plastic pieces, speaking with a plastic manufacturer is vital to make your design a reality. Blueprints and digital models are great, but they are do not account for the logistical work that will need to be done.
2. Not Prototyping & Not Having Multiple Designs
Bring professional designers into the prototyping and design iteration process early. Even if the original design seems viable, multiple iterations will help find problems as well as areas where the design can be made more efficient. The best way to save money in this regard is to work with a company with the ability to test and improve designs.
3. Not Thinking About Draft
When it comes to custom injection molding one of the most important and often overlooked parts of the design process is how the piece will be removed from the mold. Designing draft means considering design elements that will make it easier to remove the plastic from the mold without risking damage. Consider wall thickness and undercuts and how these will affect releasing the plastic piece from the mold. Some manufacturers use mold flow analysis software to find weaknesses in how the plastic will interact with the mold.
4. Not Using The Right Type of Mold
Most companies that have settled on a design use metal molds that are designed to produce thousands of perfect plastic pieces quickly. However, if you are in the prototyping phase, you will not need a highly durable mold designed to make thousands of pieces until you have settled on both your part design and the mold design. Work with manufacturers to develop cheaper molds in the prototyping process before increasing your budget for high durability long-lasting molds.
5. Not Using The Right Materials
One of the most common problems in plastic manufacturing is manufacturers not using the best plastic material. Choosing the right plastic material is the best way to get the most for your money. Work with experienced manufacturers and do your research. There is a large variety of options out there, and knowing the right materials for your needs goes a long way.
Lee’s Plastics Inc. has over 100 years of combined experience in the plastic manufacturing industry. If you need help engineering your prototype, choosing materials, designing your mold, we can help. Give us a call or contact us to learn more about our services.