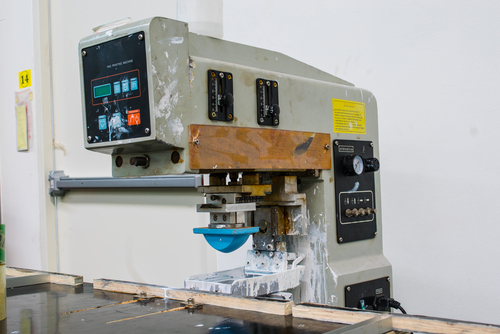
Lee Plastics works on a variety of plastic parts for many different clients throughout different industries. Aside from creating thousands of plastic components, we also provide many different value-adding services to each of our clients. These include pad printing and hot stamping. Both of these processes allow us to place images on plastic components.
What Is Hot Stamping
Hot stamping is the process of using heat to transfer a two-dimensional image onto a three-dimensional plastic component. It uses foil and a die. For curved surfaces, the die is made with silicone so that it can bend. For flat surfaces, the die is usually made of magnesium or another metal that lies flat. First, the design is imprinted on to the die which ensures that there is a clean transfer from the die to the plastic piece. Then the die is heated and a ribbon of foil is placed between the hot die and the plastic piece. The ribbon is left behind in the shape of the design on the piece. Hot stamping is great for quick production speeds and rarely has issues.
What Is Pad Printing
Unlike hot stamping, pad printing uses an indirect offset printing process. Instead of using foil and heat, pad printing uses inks. A silicone pad is pressed against an insert that lifts the ink in the shape of your design. The ink is then pressed onto the plastic component which creates the logo image.
What Are The Pros and Cons of Both Methods
Hot stamping is by far ideal for flat or gently contoured surfaces. The flatter the surface, the easier it is to transfer the foil. Because hot stamping doesn’t utilize ink, there is no chance of running or smudging in the design. It is also easier to print a multi-color design quickly with hot stamping. Pad printing is best for transferring images onto complex three-dimensional surfaces. This includes products with textured surfaces or irregular shapes. For instance, a golf ball would be a great candidate for pad printing. Pad printing uses ink, so there is a chance of a smudging compared to hot stamping. Although a manufacturer like Lee Plastics can avoid these problems by making sure that machines are calibrated correctly, and that only perfect models are sent to the client.
Contact Lee Plastics
If you need a complex plastic piece made or need something printed on to your mass-produced goods, contact Lee Plastics Inc. We would be happy to bid on your project and provide you an estimate for our work. We are dedicated to quality and meeting all of our client’s standards.